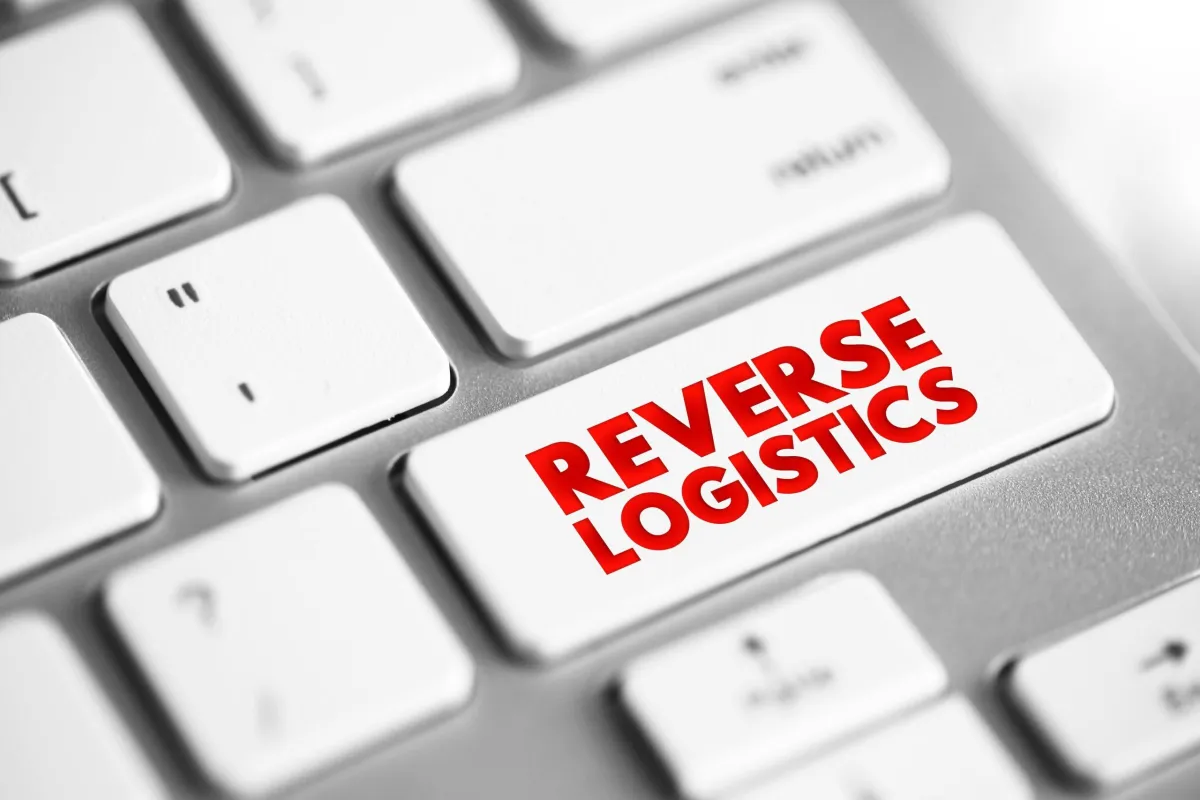
Reverse Logistics: A Competitive Edge in Modern Supply Chains
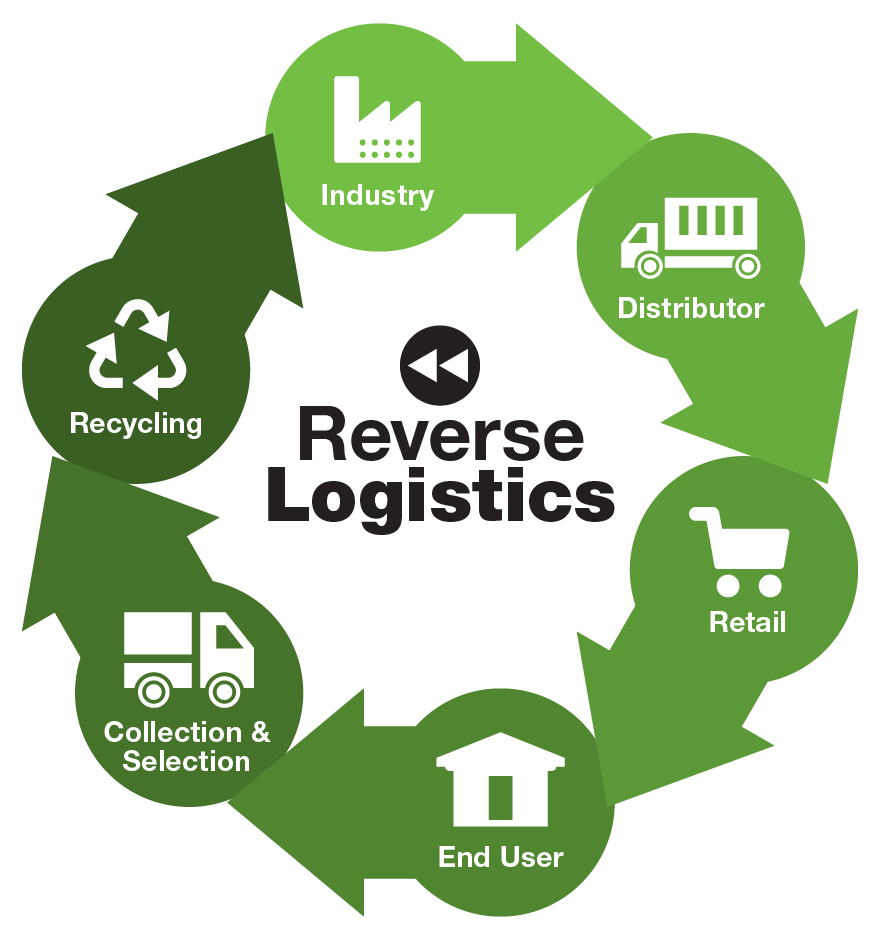
Reverse Logistics: A Competitive Edge in Modern Supply Chains
In today’s rapidly evolving business environment, companies face increasing pressure to optimize their supply chains not only for efficiency but also for sustainability and customer satisfaction. One key area that has gained significant traction over the years is reverse logistics. While traditionally, logistics has been associated with moving products from manufacturers to consumers, reverse logistics focuses on the opposite: the flow of goods from customers back to the company.
The Origin of Reverse Logistics
The concept of reverse logistics emerged from the need to manage returned products. In the past, returns were often seen as a costly inconvenience. However, as industries grew more complex and customer expectations evolved, businesses started recognizing the value in recapturing, reusing, and recycling products. The rise of e-commerce in the late 1990s and early 2000s further accelerated the need for robust reverse logistics systems, as return rates for online purchases soared compared to in-store purchases.
The term "reverse logistics" was formally coined to describe this process of handling product returns, repairs, refurbishing, recycling, and disposal. It became a critical part of the supply chain, where companies could leverage the function not only to reduce waste but also to unlock additional value in returned or defective goods.
How Reverse Logistics Makes Companies Competitive
Integrating reverse logistics into a company’s operations can lead to several competitive advantages:
Cost Efficiency: Effective reverse logistics helps companies recover value from returned products through resale, repair, or recycling. Instead of discarding defective items, businesses can refurbish and resell them, often at a lower price, thus increasing revenue streams. This also reduces costs associated with waste disposal.
Sustainability: As environmental consciousness grows, consumers are increasingly favoring companies with sustainable practices. Reverse logistics enables companies to reduce their carbon footprint by reusing materials, recycling products, and minimizing waste. A strong sustainability strategy not only enhances brand reputation but also opens the door for government incentives and compliance with environmental regulations.
Improved Customer Satisfaction: An efficient returns process is essential in today’s competitive market. Customers expect hassle-free returns, and companies that excel in this area build trust and loyalty. Reverse logistics allows businesses to handle returns quickly, provide refunds or exchanges seamlessly, and create a more positive customer experience.
Data and Insights: By analyzing return patterns and the reasons behind product returns, companies gain valuable insights into their manufacturing, quality control, and customer preferences. This data can help identify product flaws, improve future designs, and enhance overall product quality.
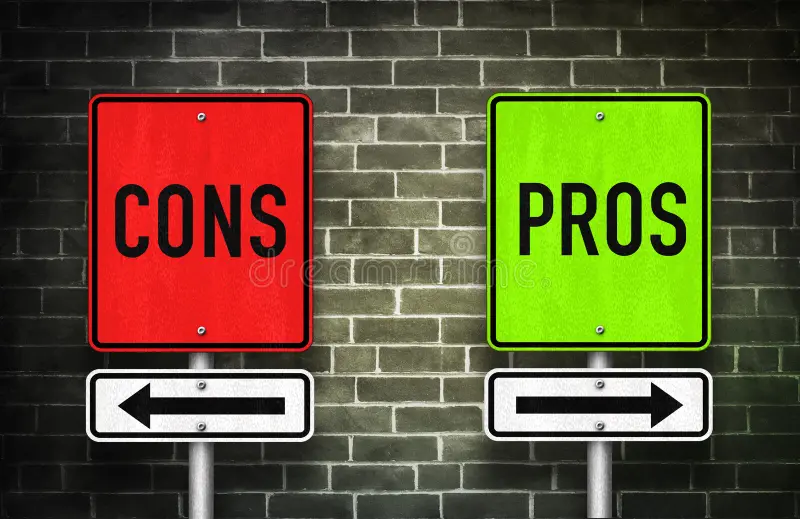
Pros and Cons of Reverse Logistics
Pros:
Resource Recovery: Companies can recover usable materials, reducing the need for raw resources and minimizing production costs.
Environmental Impact: Reverse logistics helps companies become more sustainable, which can lead to long-term cost savings and improved public perception.
Competitive Differentiation: Companies with strong reverse logistics processes stand out in the marketplace for their ability to manage returns, repairs, and recycling efficiently, enhancing their overall service offering.
Cons:
Complexity and Costs: Implementing reverse logistics requires significant investment in infrastructure, technology, and human resources. The complexity of managing multiple return channels, handling defective goods, and processing them can be costly.
Inventory Management Challenges: Tracking returned items and reintegrating them into inventory can be difficult, particularly when managing large volumes of returns. This can lead to inefficiencies in the supply chain and longer lead times for processing.
Fraud and Abuse: Return fraud, where customers exploit return policies, can be a significant issue. Companies need to implement robust systems to detect and prevent fraudulent returns.
Conclusion
Reverse logistics has evolved from a mere afterthought to a key strategic function that drives competitiveness in today’s market. While there are challenges to managing reverse logistics, the benefits—cost savings, sustainability, improved customer satisfaction, and enhanced brand loyalty—make it a vital component of modern supply chains. Businesses that invest in optimizing their reverse logistics processes will be well-positioned to gain a competitive edge, reduce waste, and create a more sustainable future.